IFP DPM EPOXY is a two-pack, solvent-free epoxy-based
coating designed to be used as a damp-tolerant primer
and damp-proof membrane, for use with the IFP Resin
Systems range of surface coatings and toppings.
DPM EPOXY suppresses residual construction moisture and rising
dampness in concrete and sand/cement screeds and can be
used in situations where the relative humidity level is above
75%. It is applied by brush or roller in a one, two or three-coat system. IFP DPM is also available in a fast-cure.
Available Colours
IFP DPM is available in Clear
Product Advantages
Moisture tolerant
Moisture suppressant Excellent adhesion
Good chemical resistance
Typical Areas of Usage
To be used as a primer for concrete and sand/cement
screeds with a residual moisture level greater than
75%RH prior to the application of Epoxy Resin and resilient
floor systems Where levels between 85 and 95 % RH are
encountered a minimum of two coats must be applied and
above 95% RH a minimum of three coats.
Curing Schedule at 20 ̊C
Pot Life 30 minutes 15 minutes
Pedestrian Traffic 12 hours 6 hours
Technical data after 28 Days at 20°C
Compressive Strength N/A
Shore D Hardness N/A
Bond Strength > 3.3 Nmm2(Concrete Failure)
Abrasion Resistance N/A
Slip Resistance
Pendulum Test to
BS7976-2N/A
VOC 190g/l
Based on a fully mixed unitMoisture Resistance
Up to 95% RH (Two Coat),
if recommended
dry film thickness is applied.
Surface Preparation
To be assured of maximum adhesion and best propertoes
the correct surface preparation is essential. The concrete substrate must be a minimum of
28 days old. The substrate should be sound with a minimum
compressive strength of 25 N/mmР and a minimum pull-off
strength of 1.5 N/mmР.
The surface must be clean, dry and free of contaminants
such as dirt, oil, grease, coatings and surface treatments
and contain a functioning damp-proof membrane. If in
doubt, apply a test area first. Concrete substrates should
be mechanically prepared using vacuum-enclosed abrasive
blast cleaning or diamond grinding equipment to remove
laitance and previous surface treatments followed by
thorough vacuuming leaving an open textured surface.
Weak concrete must be removed and repaired using
recommended IFP products.
Coverage Rate
Approximately 3.0 - 4.0 m2per kg per coat. Coverage
is dependent on surface profile, texture, porosity and
substrate temperature. In areas where high porosity is
encountered a further coat must be applied to achieve a
the sealed surface of minimum film thickness 190 microns per
applied coat.
Important information
This product is not a wearing finish and should be
over-coated within the application on time window.
The product should be protected from other trades using
Kraft paper or similar breathable material. Polythene
should not be used.
Protect the floor surface from mechanical damage
between coats and during installation of
subsequent finishes.
The substrate and uncured floor must be kept at
least 3°C above the dew point to reduce the risk of
condensation or blooming on the surface.
Protect the installed fl oor from damp, condensation
and water for at least twenty-four hours at 20°C.
Ensure that the ambient temperature remains above
10°C for at least twenty-four hours after installation.
Never leave the mixed IFP DPM unit to stand for
any length of time prior to application as this will result
in heating of the product and considerably shorten its
working time.
Under no circumstances must the mixed material be
left in an enclosed container as this will result in a build-up of heat and the possible release of vapours. The
mixed material must not be left unattended at any point
unit l fully cured.
IFP DPM is produced by a batch manufacturing
process, despite controlled manufacturing procedures
and tolerances, variations in colour can occur between
different batches. Products from different
batches should not be used in the same area or on
surfaces close together.
top of page
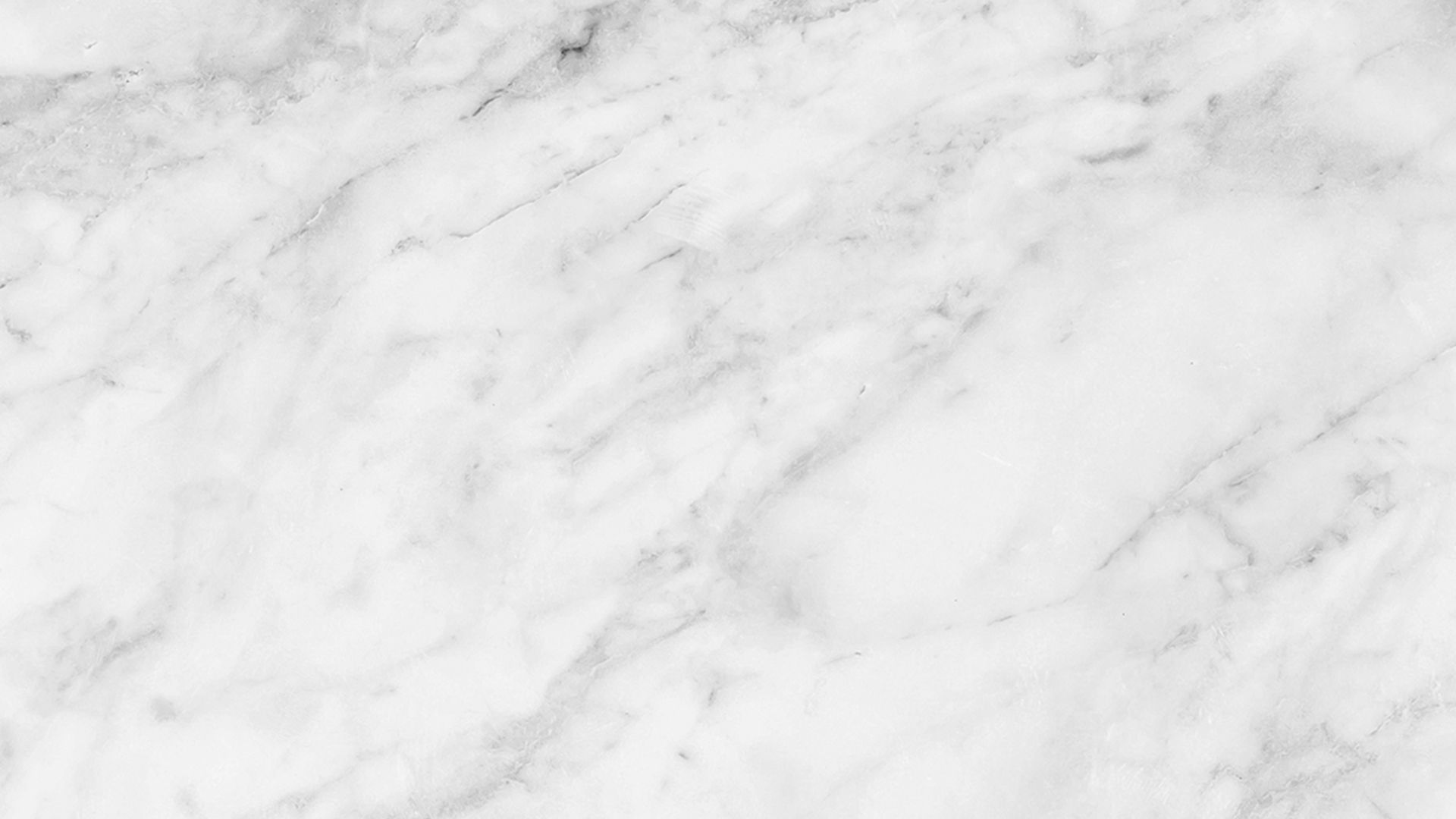

Industrial Floor Products
£595.00 Regular Price
£535.50Sale Price
Excluding VAT
Related Products
bottom of page